Environnement12 février 2023
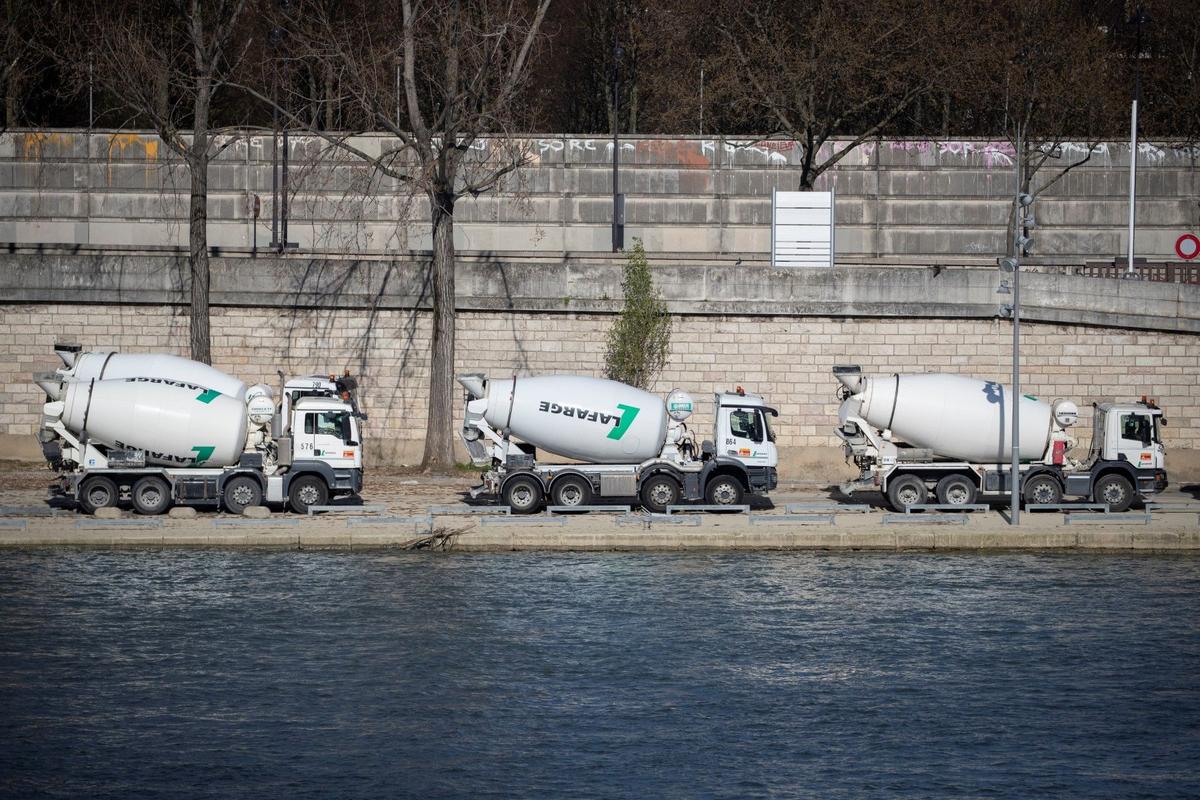
Atlantico Green
Le long chemin vers le ciment bas carbone
Depuis des milliers d'années, l'humanité vit une histoire d'amour avec le ciment et le béton. Mais aujourd'hui, les groupes industriels et les chercheurs cherchent des solutions aux énormes quantités de dioxyde de carbone que la fabrication du ciment génère.