Environnement1 janvier 2023
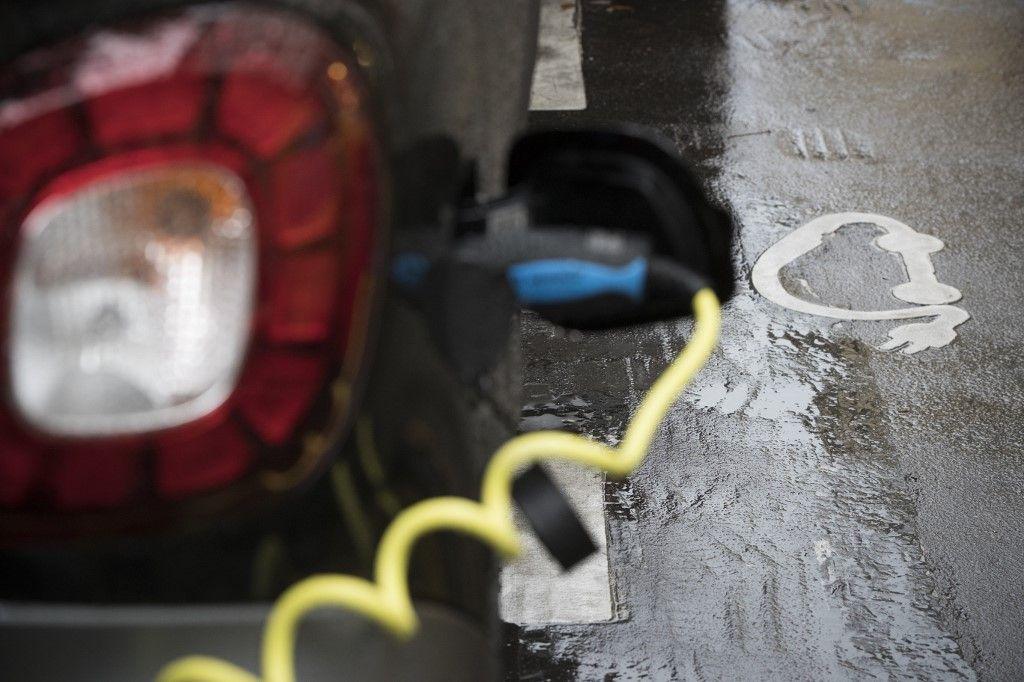
Atlantico Green
Envol des véhicules électriques : le défi du recyclage de million de batteries usagées
Au Nevada et dans d'autres États américains, des entrepreneurs anticipent le prochain boom des batteries lithium-ion hors d'usage des voitures électriques et espèrent créer un marché pour les minéraux recyclés.